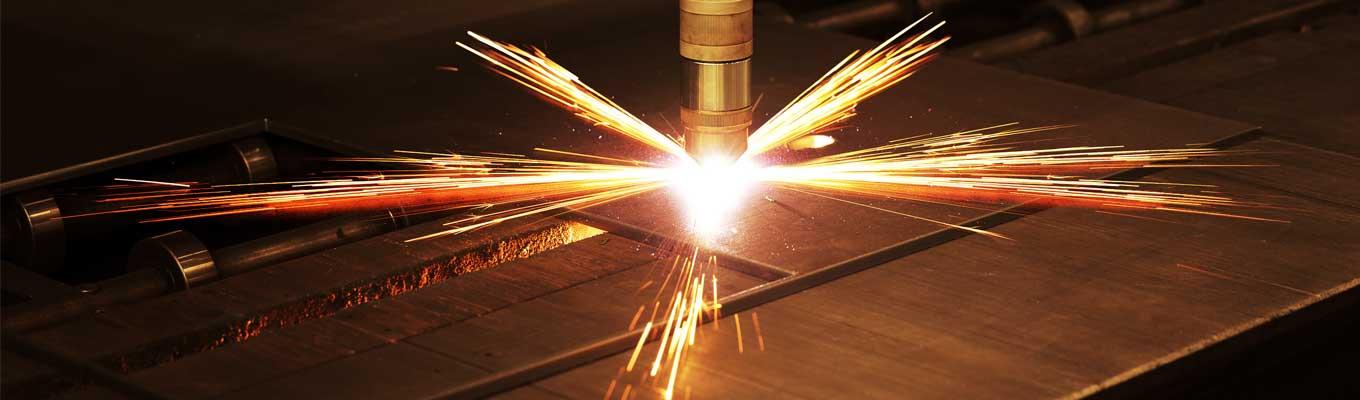
Chapas grossas ASTM A572 50 para processamento em máquinas de corte a laser de alta potência
Chapas grossas ASTM A572 50 para processamento em máquinas de corte a laser de alta potência
Diferentes métodos de corte de chapas grossas são utilizados industrialmente. Os métodos a laser, plasma, oxicorte e o mecânico são os mais comuns. O corte com jato de água de alta pressão misturada com abrasivos também pode ser eventualmente empregado (AWJ – Abrasive Water Jet).
Método |
Descrição |
Vantagens |
Desvantagens |
---|---|---|---|
Laser | Utiliza um feixe de luz altamente concentrado para realizar cortes precisos | Alta precisão, cortes limpos e sem rebarbas | Menor eficiência em chapas de elevada espessura |
Plasma | Utiliza um jato de plasma para cortar o aço | Rapidez e eficiência no corte de chapas de elevada espessura | Pode gerar rebarbas e deformação térmica |
Oxicorte | Utiliza uma chama de gases e oxigênio para fundir e cortar o aço | Eficiente para chapas mais grossas | Menor precisão e pode gerar deformação térmica |
Mecânico | Utiliza uma lâmina para cortar o aço de forma mecânica | Simplicidade e eficiência para cortes retos | Dificuldade de utilização para cortes complexos |
Jato de agua | Utiliza um jato de água de alta pressão misturado com abrasivos | Não gera calor, evitando deformações térmicas | Lento e de elevado custo |
Corte a Laser
- Menor perda por corte (maior aproveitamento da chapa).
- Maior precisão dimensional, principalmente em geometrias complexas.
- Menor Zona Termicamente Afetada.
- Operação mais segura em relação à similares com peças mecânicas móveis (serras) ou gases inflamáveis.
- Bordas de corte menos arrendondadas (maior perpendicularismo) e sem rebarbas.
Perdas de corte (kerf) típicas em chapa de aço 12,5mm
Os gráficos abaixo retirados da EN ISO 9013 (Thermal Cutting: Classification of Thermal Cuts – Geometrical Product specification and quality tolerances) representam o posicionamento dos ranges de qualidade, bem como os valores esperados para cada tipo de método de corte. Percebe-se que o corte à laser apresenta as menores tolerâncias (perpendicularidade e rugosidade) entre os três métodos citados.
Evolução do processo de corte a laser | Novo aço Gerdau
No processamento de chapas grossas no Brasil, tradicionalmente, utilizava-se o corte a laser em espessuras até 12mm, o plasma para espessuras entre 12mm e 38mm e o oxicorte em espessuras acima de 38mm.
Como o corte a laser perdia eficiência à medida em que se aumentava a espessura da chapa, fazia-se necessário um equipamento de corte a plasma.
Nos últimos anos, os principais fabricantes de equipamentos de corte a laser desenvolveram novas tecnologias e máquinas de maior potência que prometiam maior eficiência, precisão e qualidade de corte mesmo em espessuras mais elevadas.
No entanto, esses fabricantes só conseguiam comprovar a capacidade de corte de elevadas espessuras prometida pelos novos equipamentos com amostras de aço de siderúrgicas do exterior. Ao cortar chapas grossas de aço produzidas nacionalmente, os equipamentos não entregavam o desempenho esperado de produtividade e qualidade de corte.
A Gerdau com a sua já conhecida habilidade de compreensão das necessidades do mercado se associou ao CIT-SENAI MG na busca de uma solução. Assim, foi desenvolvido um novo aço que, ao ser processado nesses equipamentos de elevada potência, apresenta produtividade superior mantendo a qualidade e precisão de corte característicos do corte a laser.
Novo aço Gerdau | Superfície de corte
Para fins de comparação de desempenho, o material fornecido nacionalmente e um material importado considerado como referência pelos fornecedores de máquinas de corte a laser foram processados em um mesmo equipamento com parâmetros de processos distintos.
Produtividade Chapa Laser Gerdau x aço padrão
Nos testes realizados, a Chapa Laser Gerdau, na média, foi 1s mais rápido no corte do perímetro em relação ao material padrão.
A diferença encontrada foi considerada estatisticamente relevante e pode ser considerada como uma diferença significativa em favor da formulação da Chapa Laser Gerdau.
A diferença contabilizada tem potencial de ser maior, em favor da Chapa Laser Gerdau, se forem contabilizados os tempos de piercing e ausência de alarme de retroespalhamento durante corte do círculo interno do corpo-de-prova.
Laser x Plasma
O corte a laser, utilizando na Chapa Laser Gerdau ASTM A572 50 de 25,4mm, apresentou produtividade em média 15% maior que o corte a plasma.
Emissão de CO2 - Chapas Laser Gerdau
Método | Volume do kerf por metro linear | Massa do kerf por metro linear |
Plasma | 0.5 cm x 100 cm x 2.54 cm = 127 cm3 | 7,85 g/cm3 x 127 cm3 = 997 g |
Laser | 0.06 cm x 100 cm x 2.54 cm = 15.2 cm3 | 7,85 g/cm3 x 15.2 cm3 = 119 g |
Quanto carbono emite por metro linear cortado?
Processo | Aço | Emissão* g[CO2]/m | Emissão em um ano** (kg CO2) |
Plasma | A572-50 Padrão | 1.40 | 524 |
Chapa Laser Gerdau | 1.20 | 449 | |
Laser | A572-50 Padrão | 0.17 | 64 |
Chapa Laser Gerdau | 0.14 | 52 |
1 Máquina laser à fibra com uso de O2 como gás de assistência
* 100% de carbono do aço sofre queima completa, gerando CO2
** Estimativa de 1.3 m/min para dois turnos (16h) em um ano útil de 300d
Todos os testes realizados industrialmente e uma detalhada caracterização em laboratório da superfície de corte realizada no CIT-Senai MG foram realizados para definição da nova composição química e para novos parâmetros de processamento na laminação de chapas grossas. Assim, foi possível disponibilizar para o mercado nacional a Chapa Laser Gerdau ASTM A572 50.